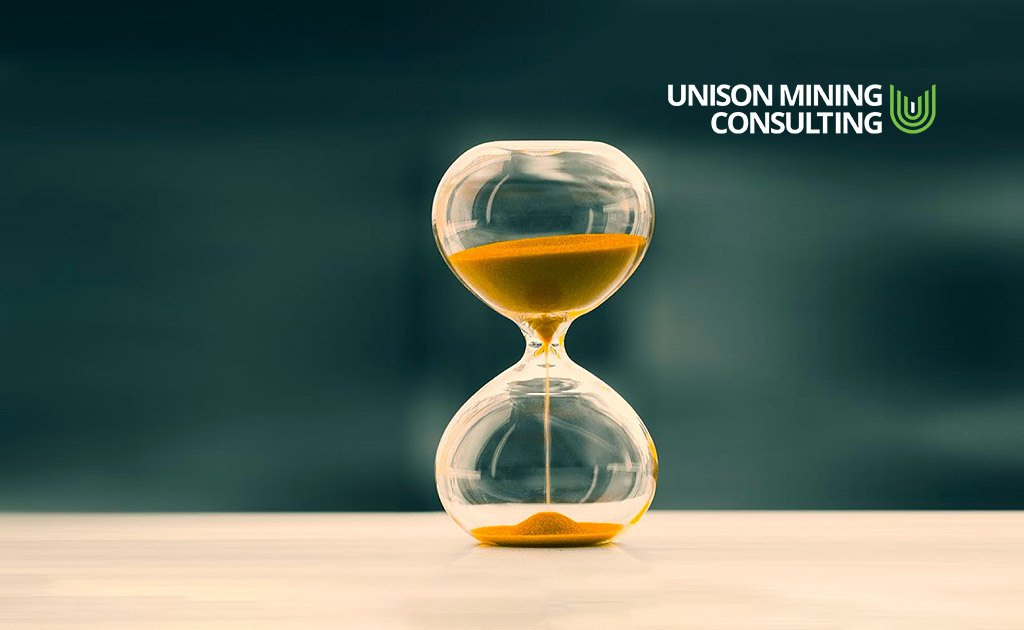
Wrench Time Optimization
Home » Value Chain » Maintenance Management » Wrench Time Optimization
Wrench Time Optimization
Overview
Optimize wrench time to reduce downtime and improve maintenance productivity
Wrench time optimization provides a huge opportunity for mining companies to improve operational efficiency, reduce downtime and lower costs. By increasing the proportion of actual time spent by maintenance technicians on repairs and maintenance activities, companies can ensure that mine productivity improves for enhanced profitability.
However, with mining equipment becoming more complex and connected through the Internet of Things and equipment sensors, the complexity of maintenance scheduling increases. Without the efficient gathering, managing and analyzing of data from monitoring systems and sensors, maintenance tasks may not be appropriately timed, which in turn leads to reduced wrench time.
For wrench time to be maximized on-site for improved productivity, comprehensive skills and training for maintenance technicians, optimal workforce scheduling, communication and coordination are crucial for success.
Key Client Challenges:
- How can we improve the skill level of our maintenance technicians through training programs or skills development?
- What strategies can we implement to ensure timely availability of spare parts?
- What scheduling methods can help us allocate maintenance tasks more effectively?
- How can we improve communication and coordination between maintenance and other departments?
- What data should we be collecting, and how can we use it to optimize maintenance schedules?
- What can we do to improve equipment accessibility for maintenance crews?
- How can we balance safety protocols with efficient maintenance processes?
Implementing new maintenance technologies, such as predictive maintenance tools and remote monitoring systems has the potential to significantly increase wrench time. However, sufficient training for maintenance technicians and management control systems are needed to monitor wrench time accurately and fully utilize these technologies.
At Unison Mining, our experts work shoulder to shoulder with your team to systematically incorporate the systems, performance metrics, and controls needed into your existing processes to ensure sustainable change.
Lacking data to validate or support key business decisions
Lack of knowledge to define a cohesive business or data strategy
Low speed to market and trouble adapting quickly to customer and market needs
High operational costs due to lengthy data processing times
OUR MAINTENANCE MANAGEMENT SERVICES
Maintenance Strategy
Wrench Time Optimization
Response Time Practices
Work Order Systems Enhancements
Equipment Aging & Bad Actors
Spares & Tools Management
Ready Backlog
Kitting & Critical Path
Subtask Time Estimation
WHY UNISON MINING
Experience
Our mining experts have experienced first-hand the day-to-day complexities and issues that arise at the mining face, giving them a higher level of understanding and insight to meet your challenges.
Practical Solutions
By implementing level-appropriate transformation tools, our behavioral and cultural change methodologies, data management, and analytics, our goal is to create a sustainable and positive impact on your mining operations.
Results-driven
We go beyond strategy to offer a direct and measurable approach to success. Our commitment extends to delivering real business outcomes and helping your team sustain those changes for the long haul.